What are Twist Drills?
Twist drill is a generic term for various types of drills, such as metal drills, plastic drills, wood drills, universal drills, masonry and concrete drills. All twist drills have a common characteristic: The helical flutes that give the drills their name. Different twist drills are used depending on the hardness of the material to be machined.
By helix angle
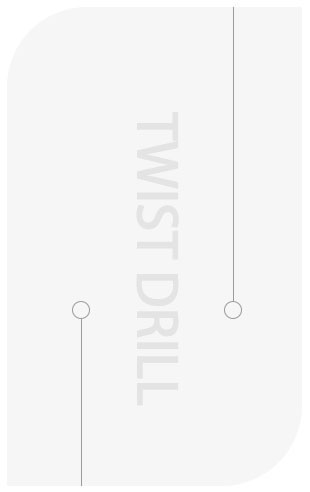
Type N
● Suitable for normal materials such as cast iron.
● The type N cutting wedge is versatile due to its twist angle of approx. 30°.
The point angle of this type is 118°.
Type H
● Ideal for hard and brittle materials such as bronze.
● The type H helix angle is around 15°, which results in a large wedge angle with a less sharp but very stable cutting edge.
● Type H drills also have a point angle of 118°.
Type W
● Used for soft materials such as aluminium.
● The helix angle of approx. 40° results in a small wedge angle for a sharp but comparatively unstable cutting edge.
● The point angle is 130°.
By material
High Speed Steel (HSS)
The material can be roughly divided into three types: high-speed steel, cobalt-containing high-speed steel and solid carbide.
Since 1910, high-speed steel has been used as a cutting tool for more than a century. It is currently the most widely used and cheapest material for cutting tools. High-speed steel drills can be used in both hand drills andamore stable environment such as a drilling machine. Another reason why high-speed steel lasts for a long time may be because high-speed steel cutting tools can be reground repeatedly. Due to its low price, it is not only used togrind drillbits, but also widely used in turning tools.
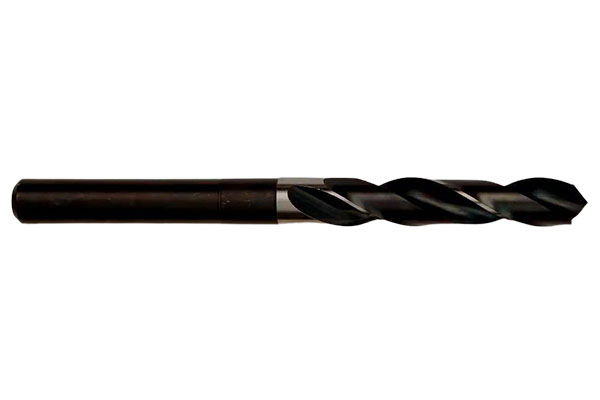
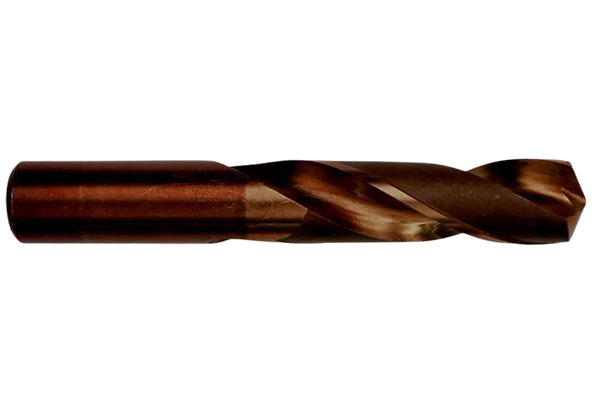
Cobalt-Containing High-Speed Steel (HSSE)
Cobalt-containing high-speed steel has better hardness and red hardness than high-speed steel. The increase in hardness also improves its wear resistance, but at the same time sacrifices part of its toughness. The same as high-speed steel: they can be used to increase the number of times through grinding.
Carbide (CARBIDE)
Cementcarbide is a metal-based composite material. Among them, tungsten carbide is used as the matrix, and some other materials are used as binders to sinter by hot isostatic pressing and a series of complicated processes. Compared with high-speed steel in terms of hardness, red hardness and wear resistance, it has been greatly improved. But the cost of cemented carbide cutting tools is also much more expensive than high-speed steel. Cemented carbide has more advantages than previous tool materials in terms of tool life and processing speed. In the repeated grinding of tools, professional grinding tools are required.
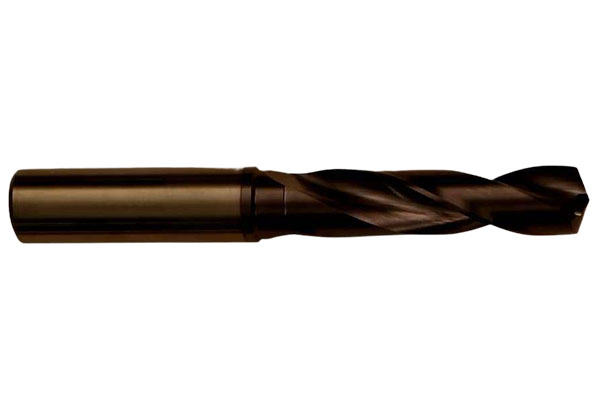
By coating

Uncoated
Coatings can be roughly divided into the following five types according to the scope of use:
Uncoated tools are the cheapest and are usually used to process some soft materials such as aluminum alloy and low carbon steel.
Black Oxide Coating
Oxide coatings can provide better lubricity than uncoated tools, are also better in oxidation and heat resistance, and can increase service life by more than 50%.
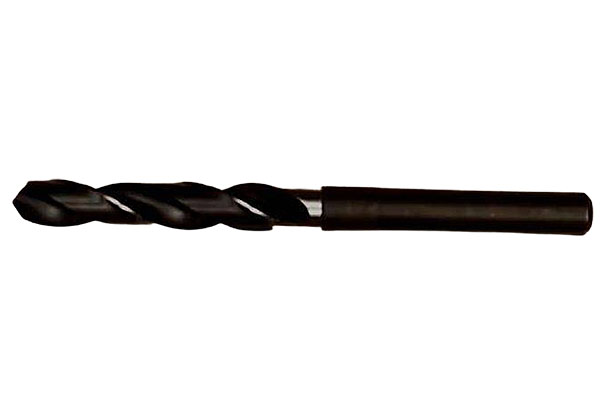
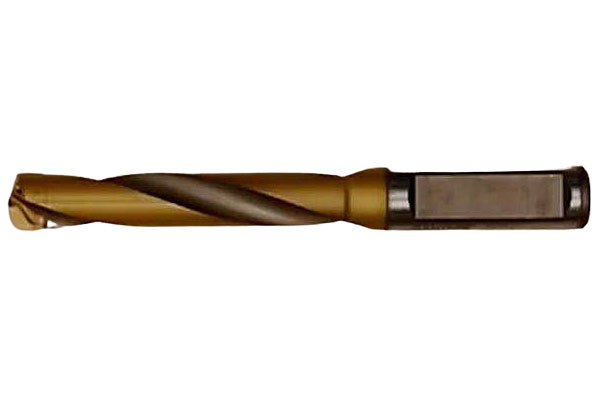
Titanium Nitride Coating
Titanium nitride is the most common coating material, and it is not suitable for materials with relatively high hardness and high processingtemperatures.
Titanium Carbonitride Coating
Titanium carbonitride is developed from titanium nitride, has higher high temperature resistance and wear resistance, usually purple or blue. Used in the Haas workshop to machine workpieces made of cast iron.
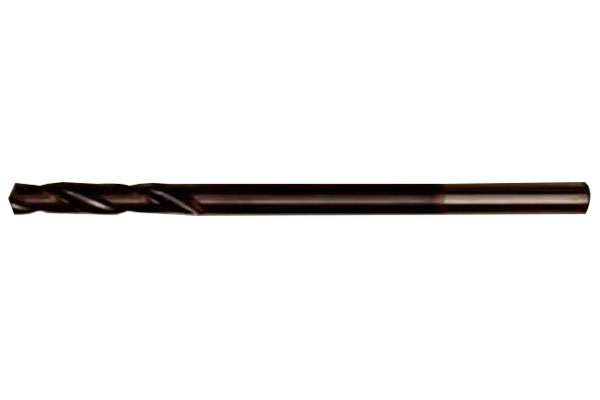
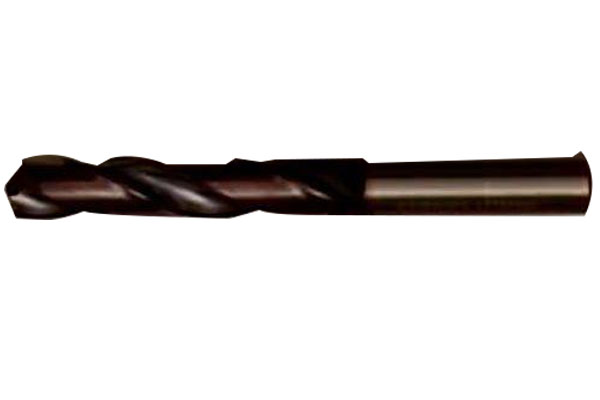
Titanium Aluminum Nitride Coating
Titanium aluminum nitride is more resistant to high temperatures than all the above coatings, so it can be used in higher cutting environments. For example, processing superalloys. It is also suitable for the processing of steel and stainless steel, but because it contains aluminum elements, chemical reactions will occur when processing aluminum, so avoid processing materials containing aluminum.
Recommended Drilling Speeds In Metal
Drill Size | |||||||||||||
1MM | 2MM | 3MM | 4MM | 5MM | 6MM | 7MM | 8MM | 9MM | 10MM | 11MM | 12MM | 13MM | |
STAINLESS STEEL | 3182 | 1591 | 1061 | 795 | 636 | 530 | 455 | 398 | 354 | 318 | 289 | 265 | 245 |
CAST IRON | 4773 | 2386 | 1591 | 1193 | 955 | 795 | 682 | 597 | 530 | 477 | 434 | 398 | 367 |
PLAIN CARBON STEEL | 6364 | 3182 | 2121 | 1591 | 1273 | 1061 | 909 | 795 | 707 | 636 | 579 | 530 | 490 |
BRONZE | 7955 | 3977 | 2652 | 1989 | 1591 | 1326 | 1136 | 994 | 884 | 795 | 723 | 663 | 612 |
BRASS | 9545 | 4773 | 3182 | 2386 | 1909 | 1591 | 1364 | 1193 | 1061 | 955 | 868 | 795 | 734 |
COPPER | 11136 | 5568 | 3712 | 2784 | 2227 | 1856 | 1591 | 1392 | 1237 | 1114 | 1012 | 928 | 857 |
ALUMINIUM | 12727 | 6364 | 4242 | 3182 | 2545 | 2121 | 1818 | 1591 | 1414 | 1273 | 1157 | 1061 | 979 |
What are HSS drills?
HSS drills are steel drills that are characterized by their universal application possibilities. Especially in small and medium series production, in unstable machining conditions and whenever toughness is required, users still rely on high-speed steel (HSS/HSCO) drilling tools.
Differences in HSS drills
High-speed steel is divided into different quality levels depending on the hardness and toughness. Alloy components such as tungsten, molybdenum and cobalt are responsible for these properties. Increasing alloy components increases the tempering resistance, wear resistance and performance of the tool, as well as the purchase price. This is why it is important to consider how many holes are to be made in which material when choosing the cutting material. For a small number of holes, the most cost-effective cutting material HSS is recommended. Higher-quality cutting materials such as HSCO, M42 or HSS-E-PM should be selected for series production.
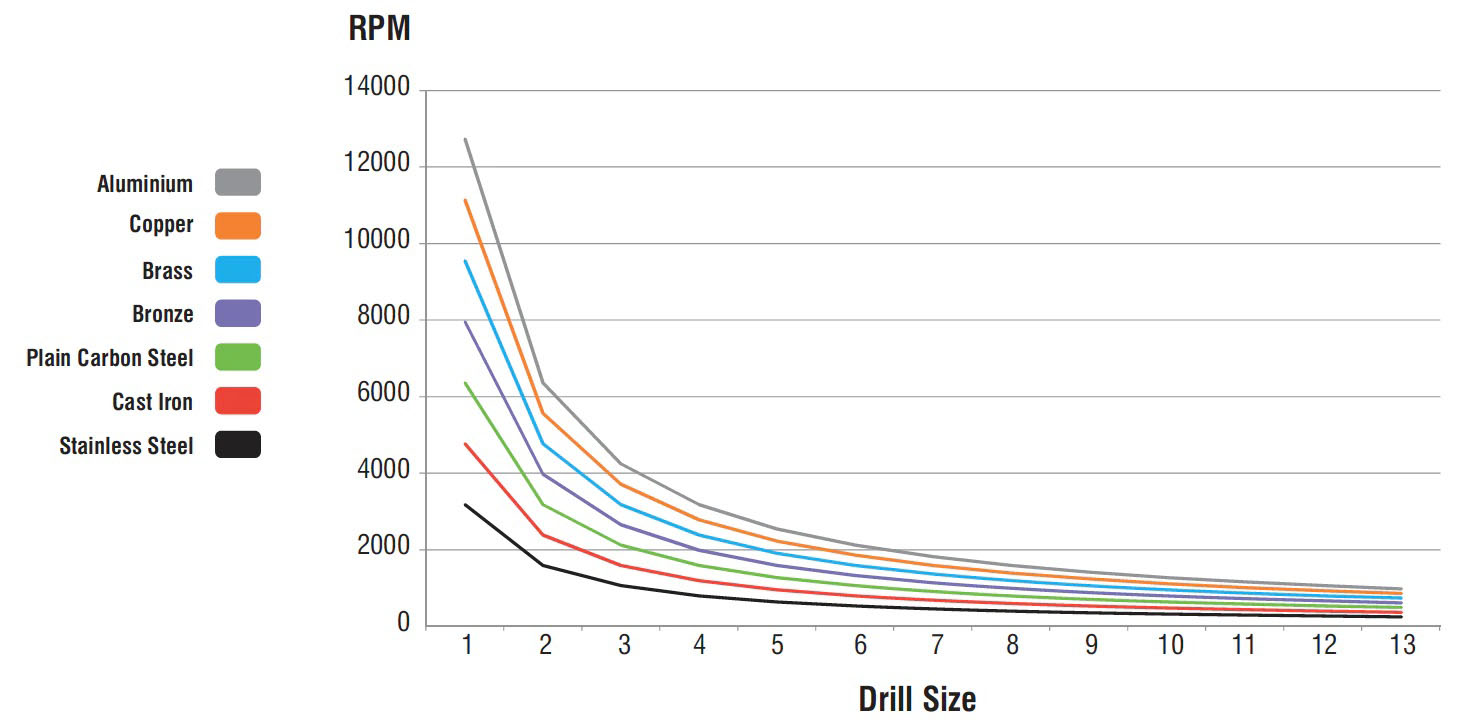
HSS grade | HSS | HSCO (also HSS-E) | M42 (also HSCO8) | PM HSS-E |
Description | Conventional high-speed steel | Cobalt alloyed high speed steel | 8% cobalt alloyed high speed steel | Powder metallurgically produced high-speed steel |
Composition | Max. 4.5% cobalt and 2.6% vanadium | Min. 4.5% cobalt or 2.6% vanadium | Min. 8% cobalt | Same ingredients as HSCO, different production |
Use | Universal use | Use for high cutting temperatures/unfavourable cooling, stainless steel | Use with difficult-to-cut materials | Use in series production and for high tool life requirements |
HSS Drill Bit Selection Chart
PLASTICS |
ALUMINIUM |
COPPER |
BRASS |
BRONZE |
PLAIN CARBON STEEL | CAST IRON | STAINLESS STEEL | ||||
MULTI-PURPOSE |
✔ |
✔ |
✔ |
✔ |
✔ |
||||||
INDUSTRIAL METAL |
✔ |
✔ |
✔ |
✔ |
✔ |
✔ |
|||||
STANDARD METAL |
✔ |
✔ |
✔ |
✔ |
✔ |
✔ |
|
|
|||
TITANIUM coated |
✔ |
✔ |
✔ |
✔ |
✔ |
||||||
TURBO METAL |
✔ |
✔ |
✔ |
✔ |
✔ |
✔ |
✔ |
||||
HSS with COBALT |
✔ |
✔ |
✔ |
✔ |
✔ |
✔ |
✔ |
Masonry Drill Bit Selection Chart
CLAY BRICK | FIRE BRICK | B35 CONCRETE | B45 CONCRETE | REINFORCED CONCRETE | GRANITE | |
Standard BRICK |
✔ |
✔ |
||||
Industrial Concrete |
✔ |
✔ |
✔ |
|||
TURBO CONCRETE |
✔ |
✔ |
✔ |
✔ |
||
SDS STANDARD |
✔ |
✔ |
✔ |
|||
SDS INDUSTRIAL |
✔ |
✔ |
✔ |
✔ |
||
SDS PROFESSIONAL |
✔ |
✔ |
✔ |
✔ |
✔ | |
SDS REBAR |
✔ |
✔ |
✔ |
✔ |
✔ |
|
SDS MAX |
✔ |
✔ |
✔ |
✔ |
✔ |
|
MULTI-PURPOSE |
✔ |
|
|
|
|